The Indian Institute of Technology (IIT) Kanpur has created a compressed air-based pipeline system for delivering coal and minerals that is both time and money efficient and offers round-the-clock monitoring.
The material loss, delivery time unpredictability, and air pollution issues will all be addressed by the cargo-based hyperloop system created by Professor Bishakh Bhattacharya and research scientists Kanhaiya Lal Chaurasia and Yashasvi Sinha at the Department of Mechanical Engineering.
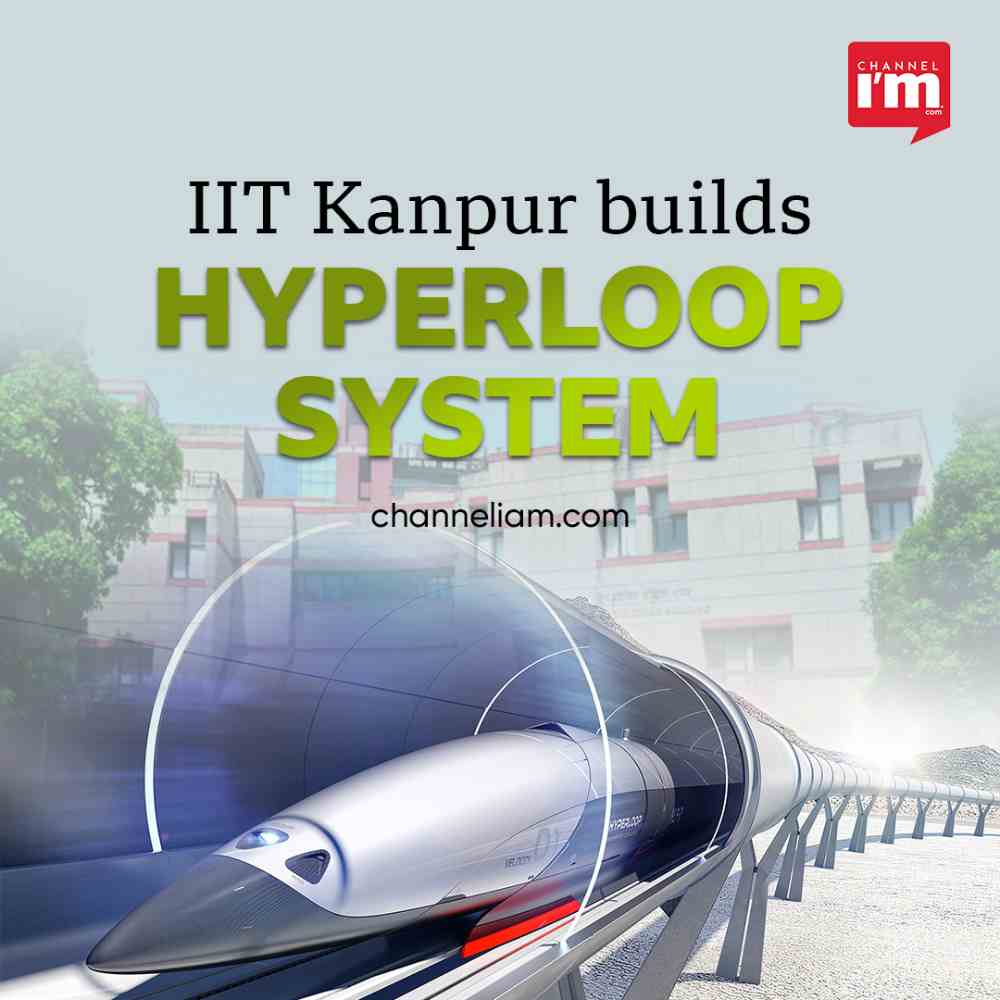
In addition to reducing transportation time, an energy-efficient pipeline infrastructure for coal evacuation, which contributes for almost 75% of India’s electricity consumption, will also lessen dust pollution at the mine sites and loading locations.
The technology was created at IIT Kanpur’s Smart Materials, Structures and Systems (SMSS) Lab, and it has already undergone a successful demonstration at the most recent UP Global Investors Conference 2023.
Hyperloop
The system uses compressed air as its power source to move coal or slurry from one location to another. According to a release from IIT Kanpur, the robot can constantly transfer the loaded block to the designated reception or discharging sub-section while moving at a speed of about 120 km/h.
Depending on the workload and necessity, more than one robotic vehicle may be running in series during this continuous operation. It claimed that even parallel pipeline loops might considerably improve transportation efficiency.
A ball and socket joint connects each module of the vehicle to the modules next to it. This gives the system connectivity and manoeuvrability, allowing the robot to navigate the pipeline network’s intricate bends.
Saving money and time
“With its dual advantage of lower energy usage and simultaneous pipeline monitoring, this technology would considerably boost production and productivity from underground and open-cast mining,” stated Abhay Karandikar, director of IIT Kanpur. The fewer trucks and railroad carriages will ease the burden on the nation’s congested freight roads and rails.
Additionally, the system offers a constant, accurate, and dependable vehicle/robot positioning system. The technology uses a hybrid multi-sensor fusion technique for waggon placement in pipes to provide such positioning performance in lengthy GPS-denied settings like tunnels or pipelines.
With a delivery rate of 5.6 tonnes per minute per km, or just 40 inches of pipe, the system uses about 107 kilowatts (KW) of power.